Combined Heat and Power at Allard Lumber Saves Money, Jobs, and Environment
February 24, 2021
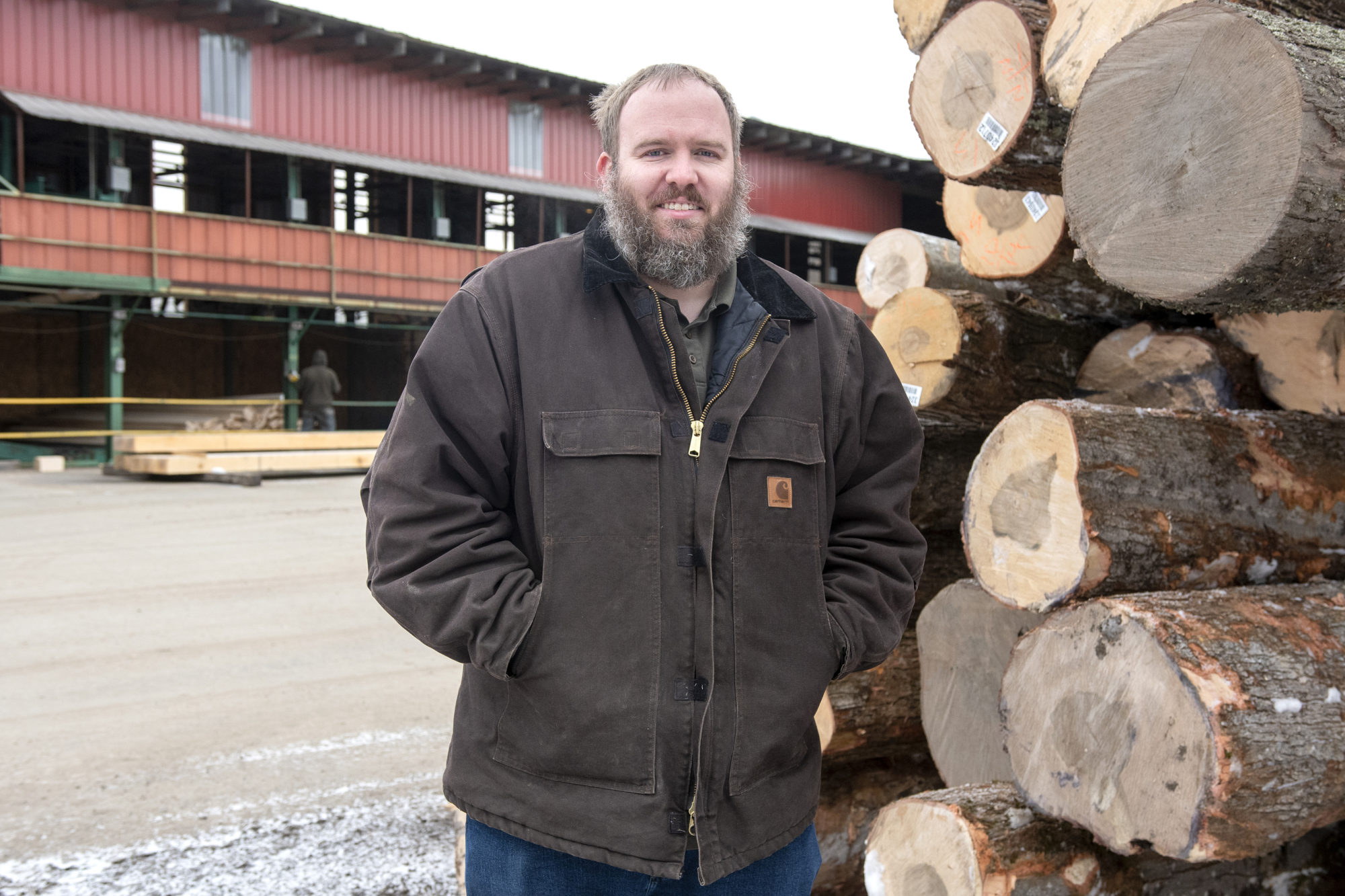
By Christine McGowan, Forest Products Program Director at Vermont Sustainable Jobs Fund
When the water pump on Allard Lumber’s boiler went a few years back, Trevor Allard finally had the excuse he needed to begin building the Combined Heat and Power (CHP) system that he had been considering for years. “I couldn’t justify throwing out a good boiler,” said Allard, “but the CHP system promised efficiency, and therefore savings, that I wanted to invest in other parts of the mill.”
One of Vermont’s oldest and largest family-owned sawmills, Allard Lumber in Brattleboro was founded by Cliff Allard, Trevor’s father, in 1974. In addition to owning several log yards, Allard kiln dries and mills lumber on site, an energy intensive operation requiring about $250,000 worth of electricity annually. Fueled with wood waste from the mill, the CHP system generates about half of the mill’s energy needs, saving the company about $160,000 annually.
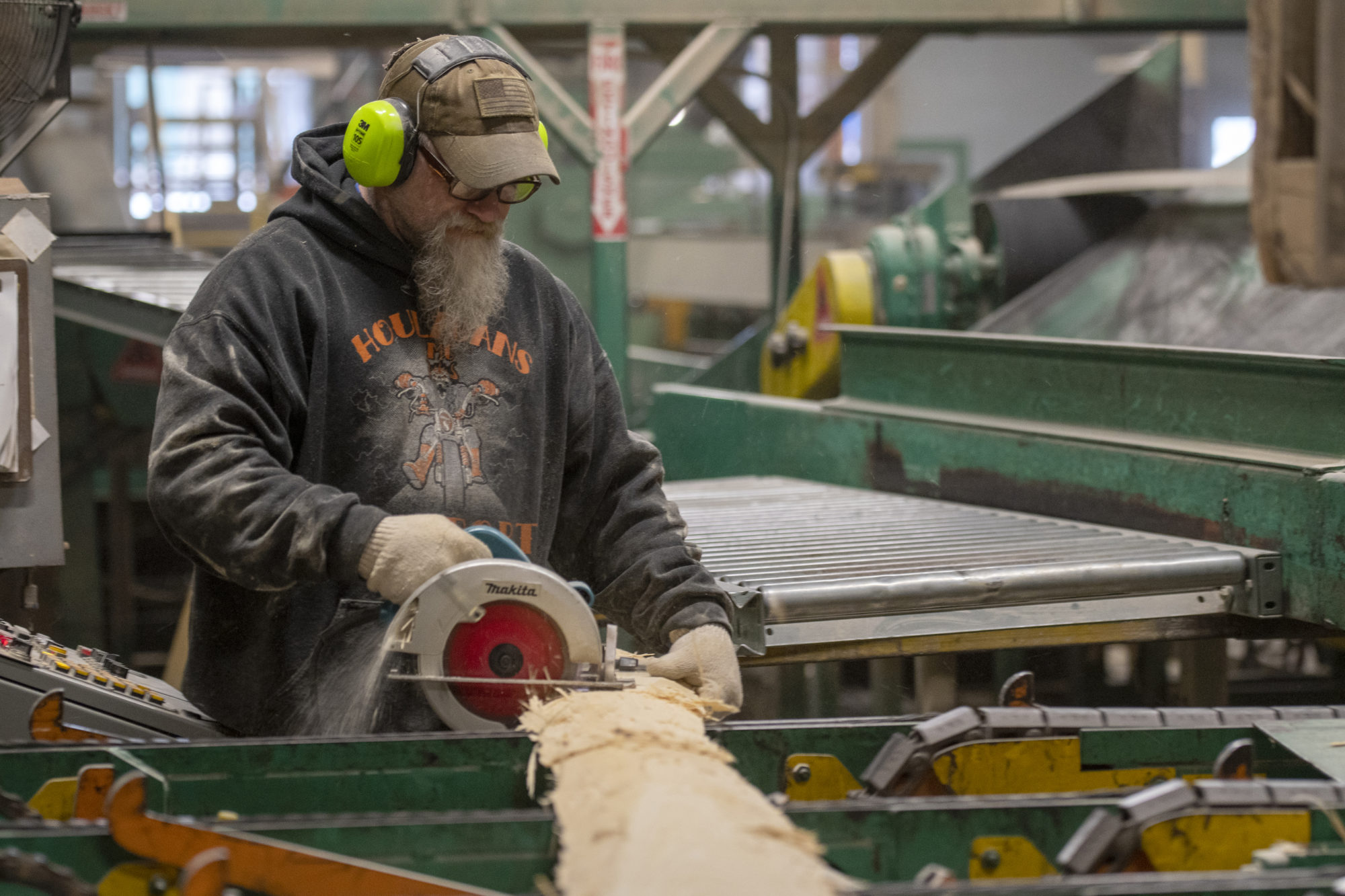
An employee works in the mill at Allard Lumber in Brattleboro, which is one of Vermont’s oldest and largest family-owned mills. Photo by Erica Houskeeper.
“Ultimately, it has made us stronger as a company,” said Allard. “Every bit of savings counts in this business, so when we save on energy costs, it means we are supporting jobs and the people who work here at the mill.”
“Allard offers a great example of how Vermont can transition to new energy sources, including the efficient and sustainable use of wood, as fossil-fuel dependent equipment reaches the end of its useful life,” said Jared Duval, executive director of the EAN. “This approach can save money and reduce emissions while supporting our local economy.”
CHP 101
According to the Environmental Protection Agency, CHP is an “energy efficient technology that generates electricity and captures heat that would otherwise be wasted.” Also known as cogeneration, CHP systems produce electricity and thermal energy concurrently, requiring less fuel than systems that produce power and heat separately. According to the EPA, conventional electricity generation wastes nearly two-thirds of the energy produced when heat is discharged into the atmosphere. A CHP system captures that heat and converts it to steam or hot water for additional energy generation. By capturing that heat, CHP systems can achieve efficiencies of up to 80 percent, compared to 50 percent for conventional technology.

Woodchips are fed into the Combined Heat and Power (CHP) system at Allard Lumber in Brattleboro. CHP systems produce electricity and thermal energy concurrently, requiring less fuel than systems that produce power and heat separately. Photo by Erica Houskeeper.
Consuming energy at the point of generation also means that less energy is lost during transmission, further improving efficiency. For Allard—and for many in the lumber industry—the fuel needed to run the CHP system is already on site in the form of wood scraps produced during normal mill operations. While it’s not “free”—Allard has to factor in the loss of revenue from selling scraps to paper mills or wood pellet manufacturers—there are no trucking expenses.
Allard’s high pressure system sends 250 pounds of steam into a turbine, which exhausts at 15 pounds. Electricity is produced from the pressure differential, leaving most of the heat in the steam. To complete the cycle, the low pressure steam is condensed back to water and pumped into the boiler, but rather than “dumping” the heat into the air as is common practice, Allard sends that heat to the kiln where lumber is dried 365 days a year at temperatures ranging from 80 to 170 degrees. That year-round demand for thermal is key to making the system efficient.
During the day, mill operations draw down more energy than Allard can produce, about 750 kilowatts an hour verses the 125 kilowatts they are able to produce, requiring them to purchase energy from the grid, but after the mill closes down at 4:00, surplus energy is sold back to Green Mountain Power and returned to the grid.
More than a monetary decision.
While capturing wasted energy yields savings that, in turn, supports the overall health of the mill, Allard also points to less tangible benefits, such as decreasing reliance on fossil fuels and supporting Vermont’s forest economy.
The main environmental benefit of combined heat and power is the reduction of greenhouse gasses that result from using less fuel. Because less fuel is burned for each unit of energy output, the process generates fewer greenhouse gasses and other pollutants.
In the context of statewide reliance on renewable energy sources, the bulk of energy demand at the mill is during daylight hours, when Green Mountain Power is able to source energy from solar. In the evenings, when demand is lower, Allard is able to generate enough power to avoid drawing down power from the grid during time periods that are often reliant on non-renewable sources of energy, such as oil, thereby helping Vermont move towards its goal of meeting 90% of total energy needs from renewables by 2050.
That’s one reason that Vermont’s Energy Development Fund gave Allard a grant for the project. Fund director Andrew Perchlik is hopeful that Allard’s story will help inspire new projects elsewhere.
“Every time we get a CHP up and running, we learn something about where this technology can be used successfully,” said Perchlik. “We want to move away from fossil fuels and Vermont has all this low-grade wood, so it can really be a win-win, especially for organizations that see themselves as part of Vermont’s working landscape.”
Supporting healthy forests, local economy.
That last point is particularly close to Trevor’s heart. Biomass-fueled CHP systems support Vermont’s forest economy by providing a market for low-grade wood. Finding markets for low-grade wood as paper mills have closed in recent years has posed a serious challenge to the industry, both in terms of revenue generation and forest management.
“In order to manage a forest properly—for species variety, wildlife, clean water, timber harvests, and overall health—loggers need a market for low-grade wood,” said Allard. “Pulling out low-grade wood so that a stand can remain healthy for decades is the right thing to do ecologically and silviculturally, but loggers aren’t making any money on those trees.”
According to Emma Hanson, Wood Heat Coordinator for the Vermont’s Department of Forests, Parks and Recreation, Vermont is currently 74 percent forested and harvesting less than half the net growth in the forest, so there is ample opportunity to source energy from wood in a way that supports a healthy forest. “It is absolutely essential to have healthy markets for both high and low grade wood,” she said. “Without the pair it is impossible to carry out a sustainable forest management plan.”
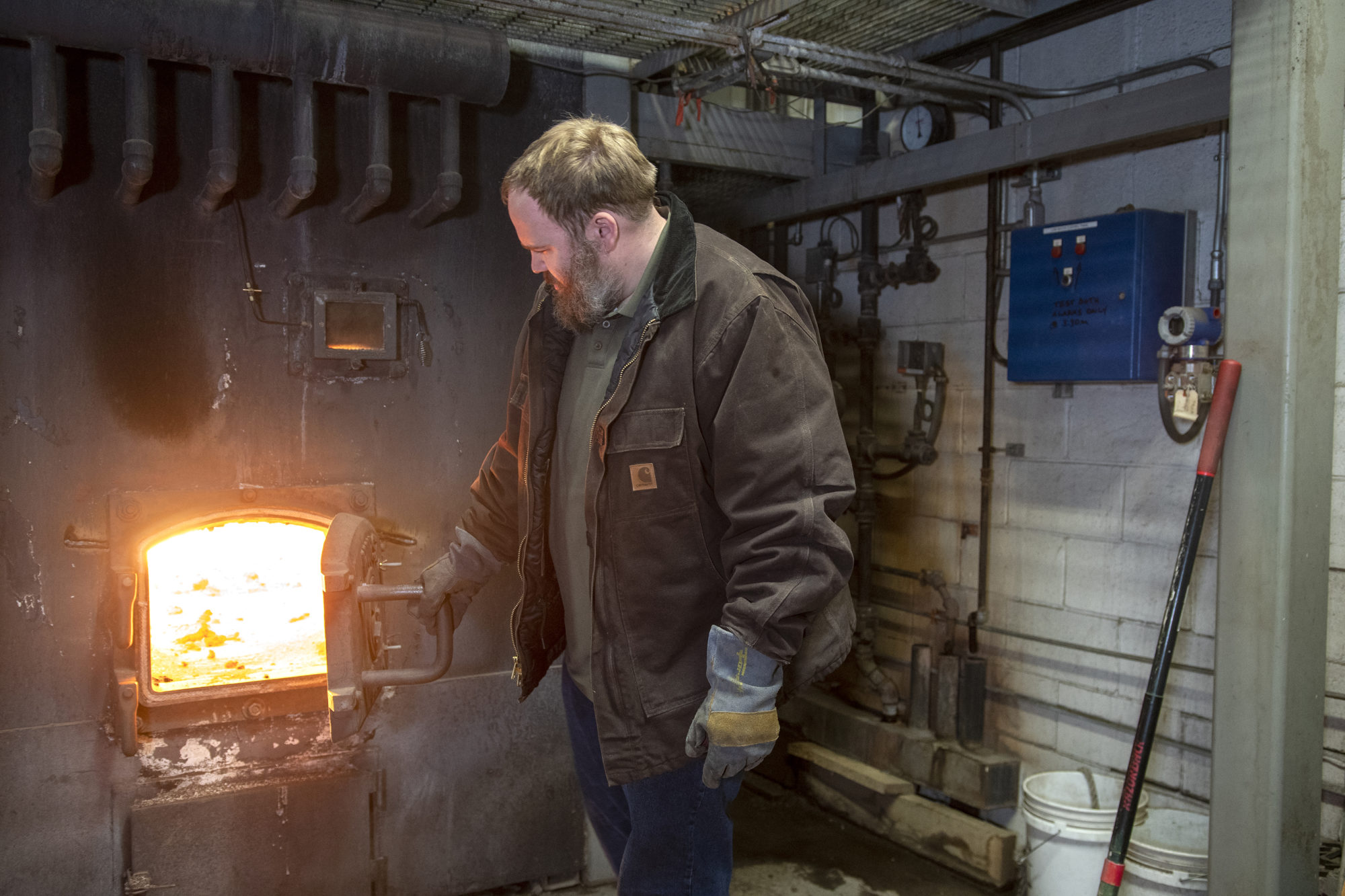
Trevor Allard checks on the boiler of the Combined Heat and Power (CHP) system at Allard Lumber in Brattleboro. The system yields 250 pounds of steam, which is sent into a turbine to heat the kiln where lumber is dried. Photo by Erica Houskeeper.
Heating with wood also keeps money in-state. A 2016 study on heating with wood found that 80 cents of every dollar spent on wood heat stays in state, versus only 22 cents of every dollar spent on oil. In 2016, that translated into an estimated $70 million retained in the Vermont economy.
“A lot of people think Vermont’s forests are being managed by big, outside corporations, but most, if not all, of the mills are locally owned,” said Allard. “We live right here and we want to do things the right way.”
About the Vermont Forest Industry Network
Vermont’s forest products industry generates an annual economic output of $1.4 billion and supports 10,500 jobs in forestry, logging, processing, specialty woodworking, construction and wood heating. Forest-based recreation adds an additional $1.9 billion and 10,000 jobs to Vermont’s economy. The Vermont Forest Industry Network creates the space for industry professionals from across the entire supply chain and trade association partners throughout the state to build stronger relationships and collaboration throughout the industry, including helping to promote new and existing markets for Vermont wood products, from high-quality furniture to construction material to thermal biomass products such as chips and pellets. Learn more or join at www.vsjf.org.
Read More Stories Like This:
- Wood Curl Packaging Reduces Waste, Supports Healthy Forests and Local Economy
- Maple Landmark, America’s “Local Toy Company,” Rooted in Family, Forest
- Loggers and Lagers: How Healthy Forests Help Brew a Better Pint
- Vermont’s Lafoe Logging Named Northeast Region “Outstanding Logger”
- Can Vermont’s Forests Help Save the Planet?